The two most common types of fire that are likely to occur at a hydrocarbon processing facility are hydrocarbon and jet fire. Hydrocarbon or ‘pool’ fires occur when a flammable liquid leaks from a vessel or pipeline to form a reservoir, which then ignites. A hydrocarbon fire will generate temperatures of up to 1100°C within ten minutes of ignition and create heat fluxes of around 150-200 kW/m2. The most common compliance standard is the UL1709 Hydrocarbon fire Ratings.
A jet fire usually involves a forceful flame, created by highly combustible fuel that is released in a particular direction as a result of a rupture to a pressurised vessel or gas line. This situation can create particularly intense levels of localised heat, plus exaggerated degrees of heat flux and turbulence, and it is far more capable of eroding fire protection measures, damaging structural steelwork and rupturing other vessels and pipework than a non-hydrocarbon blaze. Jet fire certification is done by world renowned international fire test laboratories.
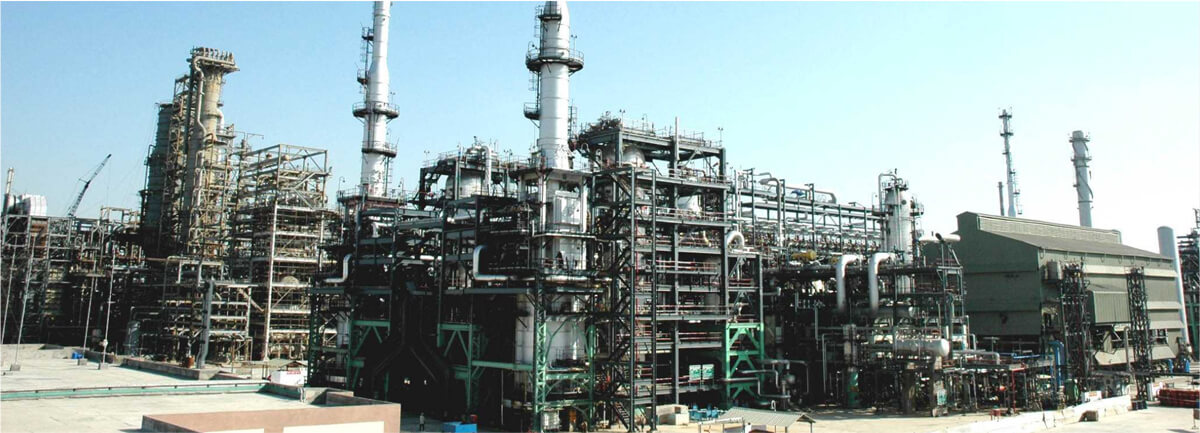
This kind of fire occurs when the fuel source is comprised primarily of cellulose material such as timber or paper. A fire of this nature has a slow flame and spreads – by comparison – gradually. This type of fire is most common in residential and commercial buildings. When the combustible material burns, it gets hot with temperatures reaching up to 500°C in as little as 5 minutes and can escalate to up to 1100°C. Its radiation value has been measured at 50 kW/m2 (Kilowatt/square meter). The most common compliance standard is the UL263& BS476-21.

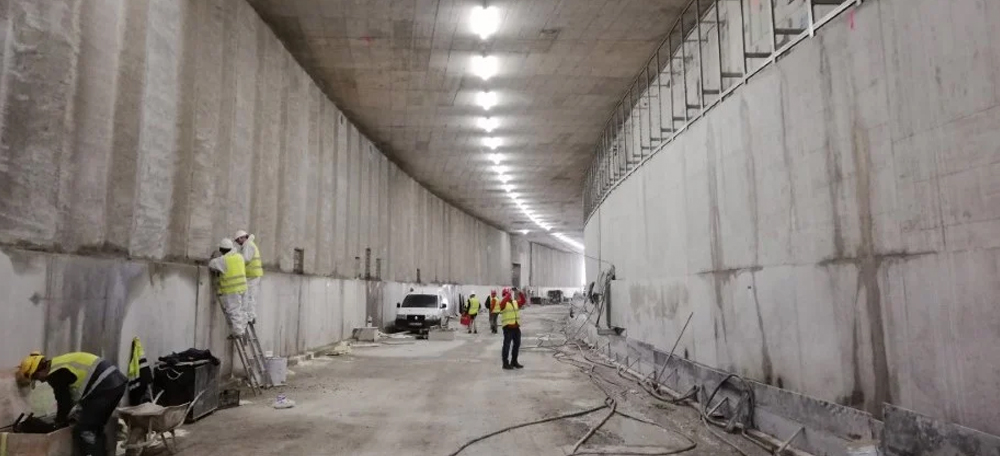
Today’s complex underground structures and tunnels must be made ready for potential incidents affecting tunnel structures and services, especially tunnel fires. Passive fire protection is vitally important for tunnels and other underground structures because the large heat release rate potential, limited escape facilities, and difficulties encountered by emergency services in gaining access for firefighting and rescue, can mean substantially increased risk factors. Providing passive fire protection will allow safe evacuation and emergency team access for firefighting. The most common compliance standard is the Rijkswaterstaat RWS heating curve
Passive fire proofing systems applied on Electric Cables are designed to prevent the spread of flame, maintain the circuit integrity of the cable for a predefined period of time and does affect ampacity of the cable because of which de-rating of the cable is not required. These systems meet all the industry test compliance standards.
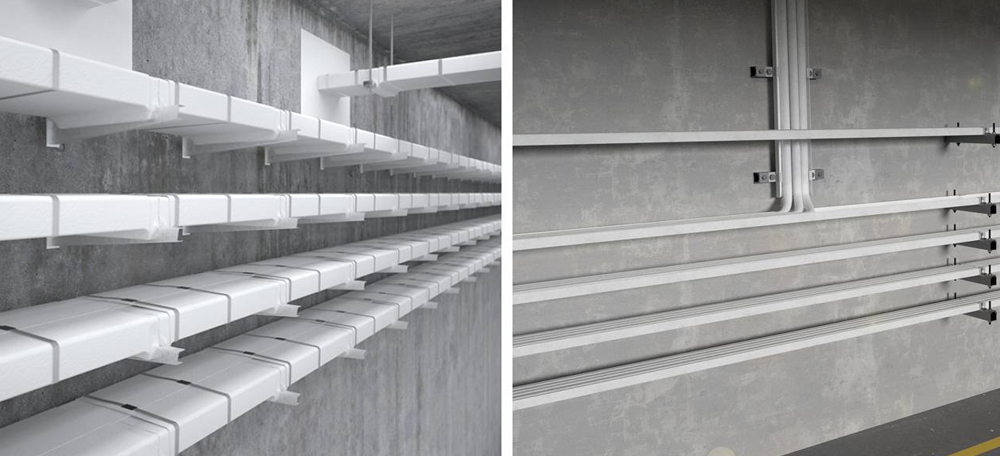